INDUCTION HEAT TREATMENT
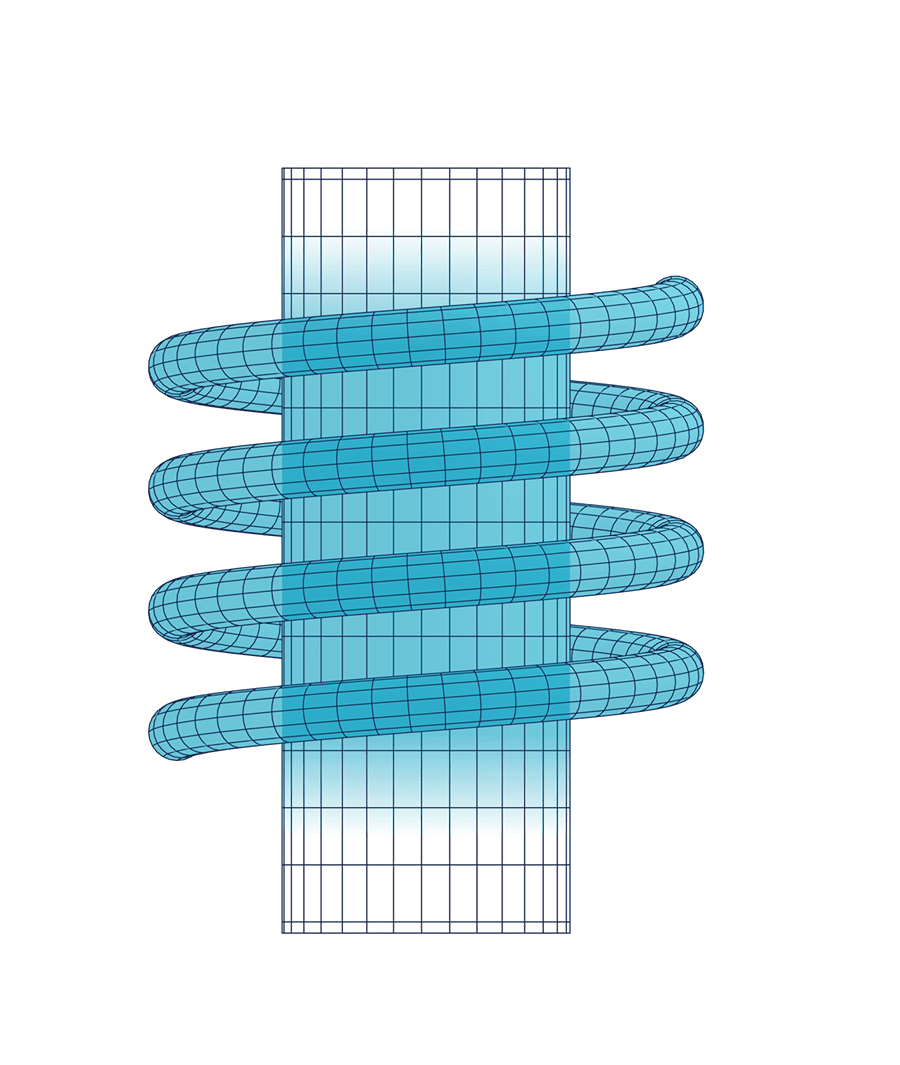
Induction heat treatment is a surface heat treatment process that uses induced current to locally heat the workpiece. It can also be applied to local or overall annealing, tempering, etc.
Induction heat treatment is a technology that utilizes the principle of electromagnetic induction to generate induced current in workpieces within an alternating magnetic field. Through the heating effect of the current, the workpieces are rapidly heated, and in combination with subsequent cooling processes, the organizational structure and properties of the materials are altered. With its advantages such as high efficiency and precision, it plays a crucial role in numerous fields, and the detailed application descriptions are as follows:
Â
- Mechanical Manufacturing Industry
- Automotive Components: For shaft parts like crankshafts, camshafts, and half-shafts in automotive engines, induction quenching can form a hardened layer with high hardness and wear resistance on the surface, enhancing their fatigue strength and service life. For example, after induction heat treatment of the journal of a crankshaft, the surface hardness is significantly increased, effectively resisting wear and ensuring the long-term stable operation of the engine. After induction quenching of automotive transmission gears, the tooth surface hardness is enhanced, improving the transmission efficiency and reliability and reducing the noise.
- Machine Tool Parts: Key components such as machine tool guides and lead screws can enhance surface wear resistance and dimensional stability through induction heat treatment. After induction quenching of the guide rails, the wear resistance is significantly improved, reducing the wear amount of the guide rails and ensuring the machining accuracy of the machine tool. Through induction heat treatment of the lead screws, not only the surface hardness is increased, but also the anti-deformation ability is enhanced, ensuring the accuracy of the machine tool’s transmission.
- Energy Industry
- Wind Power Equipment: Large components such as the main shafts and gears of gearboxes in wind turbines have extremely high requirements for strength and wear resistance. Induction heat treatment can obtain an ideal hardness and structure on the surface of these components, improving their load-bearing capacity and fatigue resistance. For example, after induction quenching of the main shaft of a wind turbine, it can withstand huge torque and bending stress, extending the service life. Through induction heat treatment of the gears in the gearbox, the risk of wear and fatigue fracture is reduced, ensuring the stable operation of the wind power generation system.
- Petroleum Machinery: Components such as drill pipes, sucker rods, and valves in petroleum extraction equipment operate in harsh environments and require good wear resistance and corrosion resistance. Induction heat treatment can strengthen the surface of these components, improving their surface hardness and corrosion resistance. For example, after induction quenching of drill pipes, the surface hardness increases, effectively resisting the friction and corrosion of downhole rocks and extending the service life of drill pipes, reducing the extraction cost.
- Aerospace Field
- Engine Components: High-temperature alloy components such as blades and turbine disks in aircraft engines have strict requirements for high-temperature strength, oxidation resistance, and fatigue performance. Induction heat treatment can precisely control the heating and cooling processes, improving the microstructure of the components and enhancing their comprehensive performance. For example, through induction heat treatment of engine blades, a fine and uniform hardened layer can be formed on the surface, enhancing the blade’s resistance to thermal fatigue and corrosion, ensuring the reliable operation of the engine under harsh working conditions of high temperature, high pressure, and high rotation speed.
- Structural Components: Structural components such as the frames and beams of aircraft fuselages need to have sufficient strength and toughness while ensuring lightweight. Induction heat treatment can locally strengthen these structural components, improving the performance of key parts. For example, induction quenching of the connection parts of the aircraft frame can enhance the connection strength, improving the reliability and safety of the aircraft structure.
- Hardware Tool Industry
- Cutting Tools: Various cutting tools such as turning tools, milling cutters, and drill bits can obtain high hardness and wear resistance on the cutting edge through induction quenching, improving the cutting performance and service life of the tools. For example, after induction heat treatment of high-speed steel cutting tools, the hardness of the cutting edge can reach 62 – 65HRC, significantly improving the cutting efficiency and durability of the tools, reducing the number of tool replacements, and increasing the machining production efficiency.
- Molds: Injection molds, die-casting molds, etc. bear large pressure and friction during operation and require good wear resistance and toughness. Induction heat treatment can strengthen the surface of the molds, improving the surface hardness and thermal fatigue resistance of the molds. For example, after induction quenching of the cavity surface of an injection mold, the hardness is increased, reducing the sticking phenomenon of plastic products and improving the demoulding performance and service life of the mold.
- Home Appliance Industry
- Compressor Components: Components such as the crankshafts and piston pins of compressors in refrigerators and air conditioners can improve surface hardness and wear resistance through induction heat treatment, reducing friction losses and improving the efficiency and reliability of the compressors. For example, after induction quenching of the crankshafts of compressors, the surface hardness is increased, reducing the wear between the crankshafts and bearings, reducing the operating noise, and extending the service life of the compressors.
- Motor Rotors: Parts such as the journal and end rings of motor rotors can enhance their surface strength and electrical conductivity through induction heat treatment. For example, after induction quenching of the journal of a motor rotor, the surface hardness is increased, improving the wear resistance and fatigue resistance of the journal. Through induction heating welding of the end rings, the welding quality is high, the electrical conductivity is good, and the operating efficiency of the motor is improved.