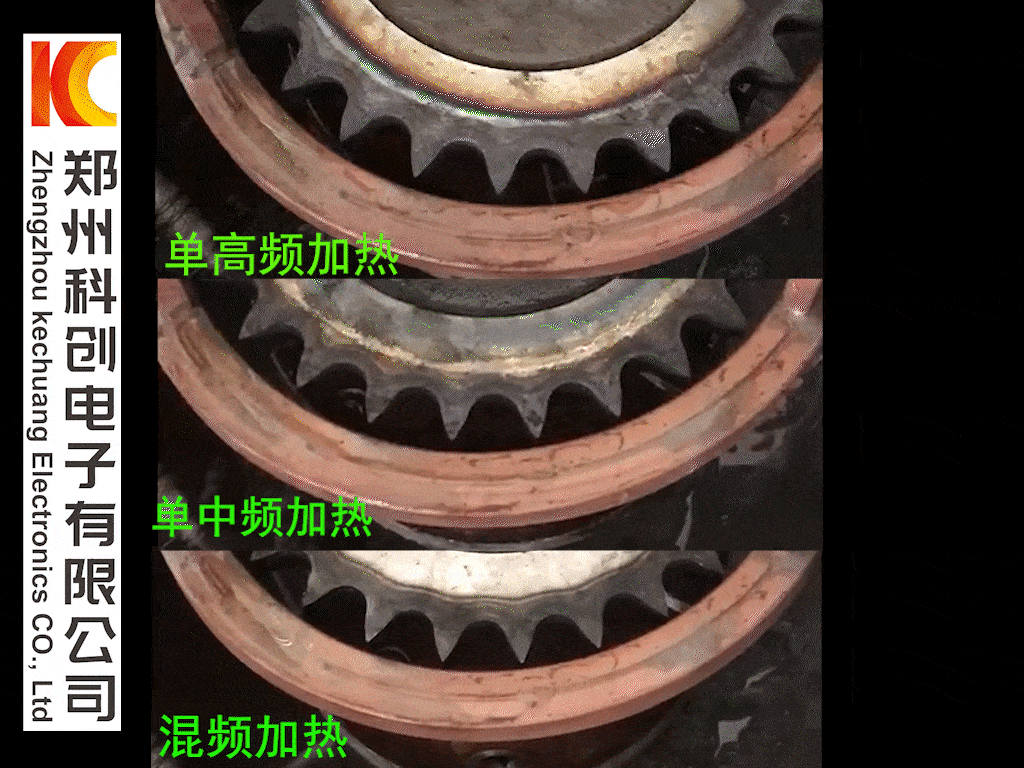
Multi-frequency induction heating Generator for gear hardening is a real-time synchronous dual-frequency induction heating power Generator . It preheats the tooth root with medium frequency and heats the tooth tip with high frequency, forming a hardened layer along the tooth profile. This technology features minimal deformation and excellent reproducibility.
Characteristics of Multi-frequency induction heating Generator
- Equipment Features
- Adopts dual-frequency induction heating output mode:
- High-frequency and medium-frequency powers are independently adjustable with composite frequency output.
- Heating currents of both frequencies are simultaneously output through one heating coil, with induction power acting on the same workpiece.
- Employs the second-generation DSP intelligent induction heating system control technology.
- Offers arbitrary switching and combination of constant power, constant current/constant voltage modes for heating applications with different loads.
- Enables switching between remote control and internal control operation modes for flexible adjustment of control methods.
- Provides a load matching indication function to intuitively guide load matching selection.
- Has a device alarm status recording function for easy query of historical data.
- Implements hierarchical login for administrators and operators to prevent unauthorized personnel from modifying heating processes.
- The intelligent DSP system collects and monitors induction heating operation status and parameters (voltage, current, power, frequency, etc.) in real time. These statuses can be connected to a centralized control network via the power supply’s internal communication interface, transmitting parameters to controllers (industrial computers, CNC systems, laptops, remote control centers, etc.) to meet workshop IoT requirements.
- Adopts dual-frequency induction heating output mode: