INDUCTION WELDING
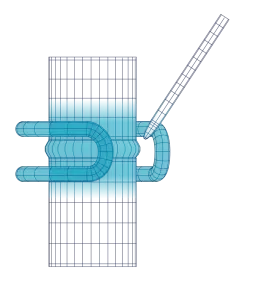
Induction welding is a welding technology based on the principle of electromagnetic induction. High-frequency alternating current is passed through the induction coil to generate an alternating magnetic field, causing the workpiece to generate eddy currents due to electromagnetic induction. Under the action of resistance, the workpiece rapidly heats up to the melting point or thermoplastic state. With the application of pressure, atomic bonding and diffusion occur, and a welded joint is formed after cooling. This technology has the advantages of fast heating, precise temperature control, stable quality, and environmental friendliness, and is widely used in fields such as aerospace, automotive, and electronics, enabling the welding of various metallic and some non-metallic materials.
Principle
- An induction coil is energized with a high – frequency alternating current. This creates a strong alternating magnetic field around the coil.
- When the workpieces to be welded are placed within this magnetic field, eddy currents are induced in the surfaces of the workpieces.
- The resistance of the workpieces to the flow of these eddy currents causes the generation of heat. The heat is concentrated in the areas where the workpieces are in contact or in close proximity, raising the temperature of the contact surfaces to the melting point or a suitable plastic – state temperature.
- As the workpieces heat up, pressure is often applied simultaneously. This pressure helps to force the molten or plastic – state materials together, allowing them to fuse and form a welded joint as they cool and solidify.
Advantages
- High heating efficiency: The induction heating process is very efficient, as the heat is generated directly within the workpieces due to the eddy currents. This allows for rapid heating, reducing the overall welding time and increasing productivity.
- Precise heat control: It is possible to accurately control the amount of heat generated by adjusting the frequency, current, and time of the induction heating. This precise control helps to ensure consistent weld quality and minimize the risk of over – heating or under – heating the workpieces.
- Clean and environmentally – friendly: Induction welding does not involve the use of open flames or consumable electrodes, which reduces the production of smoke, fumes, and other pollutants. It is a relatively clean process, making it suitable for use in various industrial environments.
- Suitable for a variety of materials: It can be used to weld a wide range of materials, including metals such as steel, aluminum, copper, and their alloys. It is also applicable to some non – metallic materials that can be heated by induction, such as certain plastics.
Applications
- Automotive industry: It is used for welding various automotive components, such as exhaust systems, fuel tanks, and body panels. The precise heat control and high – speed welding capabilities of induction welding help to improve the quality and reliability of these components.
- Electronics industry: In the production of electronic devices, induction welding is employed to join metal parts, such as the housings of electronic components, heat sinks, and connectors. The clean and precise nature of the process is crucial for maintaining the integrity and performance of these delicate components.
- Pipe and tube manufacturing: Induction welding is widely used in the production of pipes and tubes. It can be used to weld the longitudinal seams of pipes or to join different sections of tubes together. The high – speed and efficient nature of induction welding makes it suitable for large – scale production.
- Jewelry making: In the jewelry industry, induction welding is used to join precious metal components. The precise heat control allows for delicate and accurate welding, minimizing damage to the surrounding materials and ensuring the quality of the finished jewelry.