INDUCTION JOINING
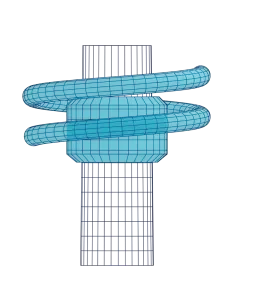
Induction joining includes disassembly and assembly is a process that uses the principle of electromagnetic induction to generate eddy currents in metallic workpieces within an alternating magnetic field, thereby heating them. By leveraging the thermal expansion and contraction properties of metals, parts are assembled or separated through heating, and a tight connection is achieved upon cooling. This process improves assembly precision and efficiency, reduces stress, and enables non-destructive disassembly.
Heat Generation through Electromagnetic Induction: When an alternating current passes through an induction coil, an alternating magnetic field is generated. A metallic workpiece placed within this magnetic field induces eddy currents due to electromagnetic induction. These eddy currents produce Joule heat under the action of the workpiece’s resistance, causing the workpiece to heat up rapidly.
Assembly and Separation Achieved via INDUCTION Heating Expansion and Contraction: By taking advantage of the INDUCTION Heating expansion and contraction properties of metal materials, the workpiece expands when heated, which facilitates assembly. After cooling, the workpiece contracts, achieving a tight connection. During disassembly, heating the workpiece again increases the mating clearance, thereby separating the components.
Induction Heating Assembly
Advantages
- Improving Assembly Precision: By precisely controlling the heating temperature and time, the expansion amount of the workpiece can be accurately regulated, enabling high-precision mating.
- Reducing Assembly Stress: It avoids the stress generated by forced pressing or hammering in traditional cold assembly, ensuring the stability and reliability of the equipment during long-term operation.
- Enhancing Assembly Efficiency: Inductive heating is rapid. Compared with traditional heating methods, it significantly shortens the heating time and boosts production efficiency. Moreover, it is easy to integrate with automated production lines to achieve automated operation.
- Adapting to Different Materials: It can be applied to the assembly between different metallic materials, such as steel and copper, aluminum and cast iron.
Application Cases
- Motor Manufacturing: For the assembly of the aluminum casing of a motor and its internal components, the aluminum casing is heated to expand it and then mated with the internal components.
- Automobile Manufacturing: The assembly of the piston and piston pin, as well as the small end of the connecting rod in an automobile engine, and the assembly of parts like gears and shafts in components such as the transmission and drive axle.
- Mechanical Manufacturing: For example, the connection of threaded fasteners, couplings, and bolts in heavy equipment such as large motors, compressors, and steel rolling mills.
Induction Heating Separation
Advantages
- Non-destructive Disassembly: It prevents damage to the workpiece caused by traditional disassembly methods and extends the service life of the components.
- High Efficiency and Convenience: The INDUCTION Heating separation process is quick and simple, improving the efficiency of maintenance and assembly.
- Good Repeatability: Multiple INDUCTION Heating disassembly and assembly operations do not affect the performance of the components.
Application Cases
- Equipment Maintenance: When maintaining equipment such as motors and automobile engines, it is used to disassemble closely mated parts, such as bearings and gears.
- Recycling and Reuse: In the field of recycling and reuse of scrap metals, it is used to separate different components of metal products, making it convenient for classified recycling and reprocessing.