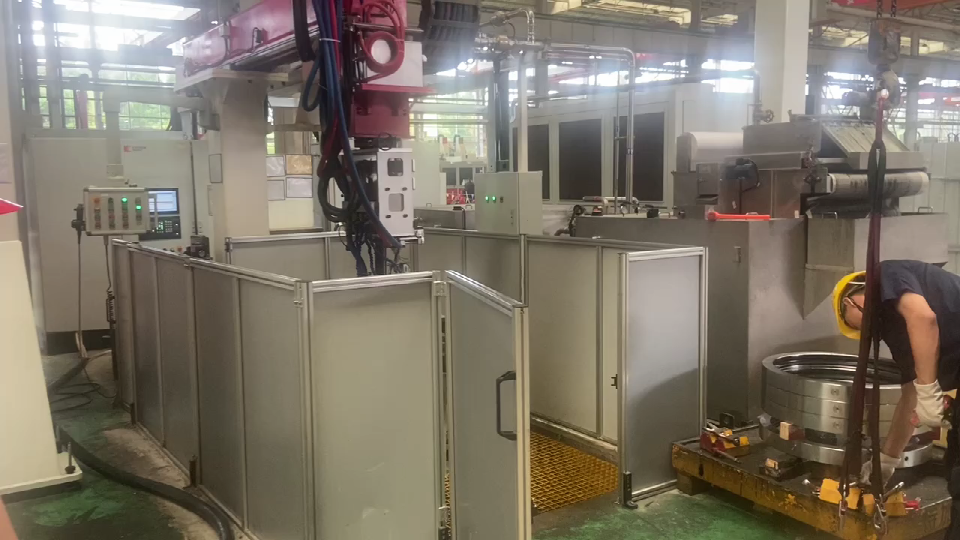
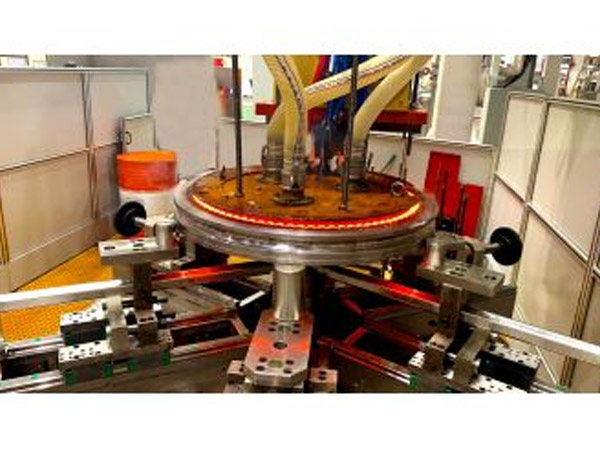
cantilever type whole-tooth CNC quenching machine tool
The cantilever type whole-tooth CNC quenching machine tool has manual operation and fully automatic operation functions. It is suitable for single-piece and batch parts production. It has functions of continuous quenching and simultaneous quenching. It is mainly used for large-scale slewing bearings, internal teeth, external teeth, tooth surfaces, etc. The overall quenching of ring-shaped parts can also be applied to the induction hardening of wheels, rings and plane parts. It is widely used in the induction heat treatment fields of wind power, automobile, engineering machinery and machine tool industries. It has reasonable structure, complete functions and convenient installation and debugging.
Equipped with a high-power induction heating output transformer, the work efficiency is high, and the equipment station layout is convenient and compact, making it easy to connect to other production lines to achieve linkage and full automation.
Structural features
The machine tool structure adopts a cantilever + rotary worktable method. The crossbeam carries the power load and can move up and down, left and right, and the workpiece is quenched at the same time;
The workpiece is laid flat, and through the 840DSL system, the load slide and the mobile CNC system realize the alignment of the induction coil and the quenching surface to achieve overall quenching of the workpiece.
The Siemens system can be used to achieve precise gap control, with an accuracy deviation of ≤0.2mm. The complete set of equipment includes a set of beams and working cantilevers, a set of heating loads, and an integrated set of induction hardening liquid spray induction coil.
Set up a manual operation interface with soft wire connection, which can be extended to 1 meter away from the load. It has power addition and subtraction, liquid spray cut-off and connection, heating cut-off and connection, displacement handwheel and other operations, making it easy for operators to adjust product models. After adjustment, the system automatically records it and no adjustment will be required for subsequent mass production.
-
DSP80KW Portable Induction Welding Machine with HHT
DSP80KW Portable Induction Welding Machine with handheld transformer
-
Special induction power supply
-
High precision parallel resonance power supply
-
MF/super audio Universal series resonance power supply
-
High precision series resonance Ultra high frequency/MF/super audio power supply
Please Feel free to give your inquiry in the form below. We will reply you in 24 hours.